Business Lessons From Hurricane Irma
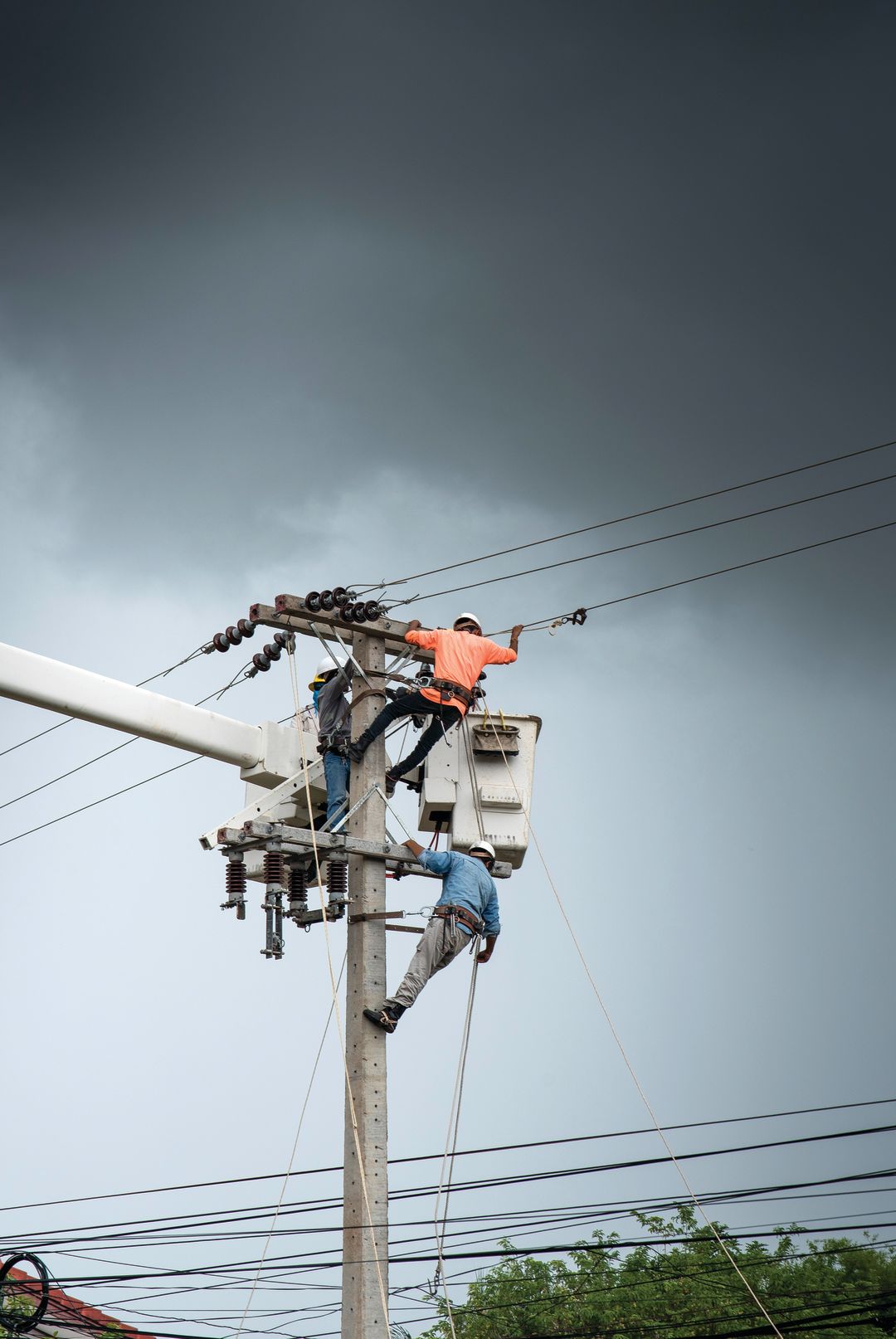
Image: Shutterstock
Todd Morton knows it could have been worse. Before its sudden turn and weakening, Hurricane Irma was set to make a direct hit on Sarasota as a major storm, causing enormous flooding and wind damage. Instead, the storm gave Sarasota a glancing blow on Sunday, Sept. 10, with no storm surge and top winds of 85 mph. But Morton, the owner of Morton’s Gourmet Market, is among many business owners for whom a near miss still turned into a big loss. He estimates the financial hit to his stores on Osprey Avenue and Siesta Key and at its commissary could reach $250,000.
“We lost power to all three of our refrigeration units over multiple days, which forced us to throw out probably $100,000 in food,” Morton says. “Our catering business also took a big hit because so many events were canceled.”
CoreLogic, a California firm focusing on business analytics, including disaster analysis, estimates that U.S. losses from Irma could reach $65 billion, over four times greater than the $15 billion inflicted by Hurricane Charley in 2004. As of Sept. 30, the Florida Department of Insurance Regulation said more than 661,000 claims had been filed in the state, including more than 100,000 from businesses.
The combined claims filed in Sarasota, Manatee and Charlotte counties totaled less than 20,000, a fraction of the claims in other parts of the state, including Dade County (66,000 claims), Lee County (42,929 claims) and Broward (45,126 claims).
Here is a closer look at how several businesses were affected by the storm and the lessons they learned.
The Chiles Group owns three waterfront restaurants, Beach House Restaurant and Sandbar Restaurant on Anna Maria and Mar Vista Dockside Restaurant and Pub on Longboat Key; they employ 350 people.
Irma’s impact: Company founder Ed Chiles says there was “zero damage” to physical structures. Power was out for four days at Sandbar on north Anna Maria, but power came back almost immediately at the Beach House and Mar Vista. “But when you close your business for four to six days, it’s expensive,” he says. “We do $100,000 on a busy day. Even during September, our slow month, when maybe we’re at 50 percent, it adds up. We also threw out $10,000-plus in food.”
How the Chiles Group prepared: COO Robert Baugh says he began communicating with staff several days before the storm to prepare and to find out which employees would be evacuating, which would be staying and which had special needs. The Chiles Group uses Hot Schedules, a platform all employees log into, to create a timeline to secure all three restaurants (since these restaurants have lots of outdoor seating and outdoor bars, it was a huge chore) and to broadcast when the restaurants would reopen. Team leaders were responsible for communicating with their members. Vendors and chefs were told earlier in the week to reduce food orders to minimize loss. Freezers and refrigerators were packed with hundreds of bags of ice.
Lessons learned: “I thought I was watching everything I had worked for in the last 37 years taken away,” says Chiles, “so we’re going to debrief to see what worked and what didn’t.” Chiles plans to contact his insurance agent and an insurance lawyer to make sure he has the proper coverage and to investigate whether generators would be a good investment. COO Baugh says his employees did everything asked of them. “People rallied to get the doors back open,” he says. “I’m proud of our team.” His task moving forward is to make sure the plywood is numbered for every door and window and to fine tune the scheduling. “I’m a calendar guy, and we can improve strategic deployment of our teams,” he says.
MyUS.com: Sarasota-based international packaging shipper with 300 employees and a 175,000-square-foot warehouse with tens of thousands of packages.
Irma’s impact: No damage to the offices or warehouse.
How MyUS.com prepared: CEO Ramesh Bulusu says employee safety came first and then customer shipments. The company began preparing on Thursday, allowing employees to leave work if they were evacuating or needed to prepare their homes or their families’ homes. Absences were excused for any employee who needed to be away, from Friday before the storm, all through the next week. Remaining employees helped secure the building, protecting the 70,000 packages in the warehouse, and were permitted to leave three hours early.
The company, which operates seven days a week, closed Saturday, Sept. 8, through Monday, Sept. 11, and employees scheduled during those days were paid for eight hours and were not required to use personal time off. The company paid for 2,879 employee hours of time while closed, totaling $40,893. MyUS also ordered lunch or dinner for all days during both weeks, especially important for employees who hadn’t had hot meals in days. MyUS purchased a $150,000 generator to make sure the business could continue to operate in power outages, but the business never lost electricity. MyUS also invested in impact-resistant windows and doors in the office portion of the business. In addition, all employees go through regular disaster training in case of any crisis in the warehouse and were able to communicate through the MyUs Work Updates Hotline.
Lessons learned: MyUS’s emphasis on employee morale—Bulusu’s motto is “Happy employees make happy customers”— and safety and disaster preparedness paid off. The business was up and running the day after the hurricane.
Dakin Dairy Farms, a family-owned dairy in business since 1973, employs 80 workers.
Irma’s impact: Storm damage to its barns and other animal quarters totaled around $250,000, says general manager Scott Cagle. In addition, production disruptions probably cost the dairy 30,000 gallons of milk. And the impact continued weeks after the storm, Cagle says, because once milk cows are thrown off their schedule they won’t return to peak production until they give birth and start a new lactation period.
What Dakin did best: “Our employees did a great job preparing for the storm, and some stayed here during the storm to get the cows milked and fed,” Cagle says. “The cows have to be milked regularly or they get sick, so the efforts our employees made were critical.”
Lessons Dakin will take forward: “We need to empty our tanks earlier and ship as much milk as we can before the storm hits.”
PGT Innovations, headquartered in Venice, is the nation’s leading manufacturer of impact-resistant windows and doors and employs more than 2,600 workers.
Irma’s impact: Company president Jeff Jackson said PGT lost power at some of its facilities, but none of its plants or inventory were damaged. In the aftermath of one of the costliest hurricane seasons ever, PGT is likely to see more demand for its products. From Aug. 17 through late September, a period coinciding with hurricanes Harvey, Irma and Maria, PGT’s stock price soared more than 18 percent.
How PGT prepared: Jackson said PGT’s leadership team checks in with every employee. A command center was set up in Naples to provide supplies, including generators and water. The company provided Family Fund Loans of $63,000, which aided 174 employees with cash, grocery gift cards, generators and chainsaws.
Lessons learned: PGT’s engineers will join a research team from the University of Florida to assess how buildings weathered the storm, helping PGT in its design of doors and windows.
Tervis, a leading manufacturer of tumblers and other drinkware, is headquartered in Venice and employs around 700 workers.
Irma’s impact: The company closed its manufacturing plant and retail stores for four days so employees could prepare and recover from the storm, says Tervis president Rogan Donelly. But none of the facilities, even Tervis’ outlet in hard-hit Key West, were damaged. Donelly says the closure put Tervis production 120,000 units behind, but that employees “have been in overdrive” since reopening and production was expected to catch up by Oct. 1.
How Tervis prepared: Donelly says Tervis emphasized communication before, during and after the storm, including checklists to protect the property and a hotline to tell employees when the plants or stores would be open, so workers weren’t traveling in adverse conditions.
Lessons learned: Donelly says the company realized its focus needed to be external, as well as internal. Tervis responded to Hurricane Harvey by partnering with Shelter Box USA, a disaster relief agency headquartered in Lakewood Ranch, to donate all net sales from Love Texas tumblers. After the storm, Tervis extended the donation program to Irma victims by donating all sales from its Love Florida tumblers. More than $10,000 has been raised.